聚合釜搅拌器的结构改造
2020-11-14 10:53:52 点击:
改造前聚合釜搅拌器的运行状况,聚合釜原搅拌器结构采用的是螺带式搅拌器,由搅拌轴和螺带式桨叶组成。搅拌转数为13r/min, 搅拌介质为含胶量56%的 ABS胶乳。由于其本身设计不足,在生产过程中存有死区,搅拌器和釜壁非常容易挂胶结垢,经常需要人工清釜,每次运转周期不足36批,每次清胶需要10h, 使生产负荷受到严重影响。由于清胶频繁,造成ABS胶乳不足,常需降低后部生产负荷,这不仅造成物料、水、人工损失,同时对连续生产和质量稳定产生严重影响,是制约连续稳定高负荷生产的主要“瓶颈”。每次清釜大约损失0.5t 粉料,且检修清釜费用较高,造成产品单耗升高,清胶后产生的高浓度COD废水,使废水预处理单元出水 COD 波动较大,影响了 ABS 胶乳产品的单耗、质量和产量。
由于影响搅拌过程的因素极其复杂,其选型既要考虑完成搅拌过程的搅拌效果,还应考虑动力消耗。在达到同样搅拌效果时,不希望消耗过多的功率;另外选型也需考虑结构,因此一个完整的选型方案必须保证效果、安全与经济。基于以上因素,在借鉴原搅拌器结构及工作原理的基础上,开发一种结构更合理的搅拌形式,以增加聚合釜的有效容积,并使返混能力增强,提高搅拌效率进而降低釜内附件上聚合物的聚结程度,使反应釜不宜结垢挂胶,延长反应釜的清胶周期及反应釜的有效运转时间。
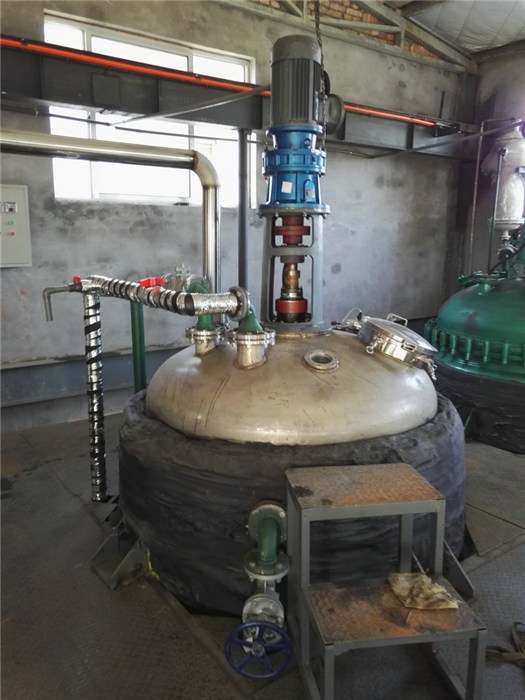
改造创新点,新型框式搅拌器结构简单,增加了聚合釜的有效容积,且具有以下特点:
b.采用S形的桨叶结构,具有增强剪切和循环作用,混合效果最佳;
c.在釜内新设置了两块折流挡板,增强了混合效果。
经过上述改造后,聚合釜在新型搅拌器的搅拌作用下,聚合物的稳定性较好,聚合过程中产生的凝聚物极少,运行效果良好。延长 ABS聚合釜的清胶周期至100d, 年减少人工清胶次数60 次,ABS粉料收率提高1.2%; 提高了聚合转化率,减少清胶损失。年减少排放COD较高的清胶废水6000t; 改造后平均每年可增加 ABS 聚合批数80批,增产 ABS 粉料1100t; 每年为工厂增创直接效益700万元;消除了制约 ABS 装置生产、消耗、质量的“瓶颈”, 为装置的连续稳定高负荷生产奠定了基础。
- 上一篇:机械搅拌澄清池运行优化重点 [2020-11-15]
- 下一篇:新型高密度澄清池 [2020-11-13]